- 首頁
- Applications
- Hydraulic System for Machining Center
Hydraulic System for Machining Center
Challenges of Traditional Hydraulic Systems in Machining Centers (MC)
Main Applications of Hydraulic Powerpack System:Tool Magazine Tool Change、Spindle Braking、Hydraulic Workholding (Hydraulic Fixtures)
Challenges:
- Instant High Flow Demand:
During tool changes and workholding, a high hydraulic flow is required instantly. However, traditional hydraulic units respond slowly, reducing machining efficiency. - Hydraulic Stability Affects Machining Accuracy:
A significant pressure drop can weaken workholding force, leading to reduced machining accuracy and poor surface quality. - Large Space Occupation:
Traditional hydraulic systems require additional cooling units to prevent overheating, and the oil tank is large, affecting the overall machine layout.A larger oil tank increases hydraulic oil consumption during each oil change, leading to higher maintenance costs.
Benefits of Switching to ANYPOWER Servo Hydraulic System:
- Ultra-fast response (0.01s
- Minimized pressure drop, resulting in enhanced machining accuracy and surface quality.
- No additional cooling system required, eliminating the cost and energy consumption of an oil cooler. Compact oil tank design, reducing machine footprint, CO₂ emissions, and hydraulic oil consumption during oil changes.
Background
- Test Machine: Horizontal Machining Center.
- The machine underwent maintenance and had Anypower servo hydraulic units installed.
Point
- The size of the oil tank for the old hydraulic equipment was reduced from 151L to 60L.
- The motor for the old hydraulic equipment was reduced from 7.5HP to 5HP.
- Temperature rise, vibration values, and current values all decreased according to actual measurements.
- The vibration value for the old hydraulic equipment decreased from 8.5u to 3.8u.
- There have been no maintenance records to date.
※ The reduced oil tank size leads to lighter weight and indirectly lowers carbon emissions.
※ Zero maintenance means zero service costs, saving company expenses.
Background
-
Test Machine: Gantry Machining Center.
- The machine originally used our VANE-type hydraulic unit. It was upgraded to our servo hydraulic unit.
No other components except the hydraulic unit were changed.
Point
-
The oil tank size was reduced from 130L to 60L after replacing the hydraulic unit.
-
The motor capacity was reduced from 5.5kW to 3.7kW (approximately from 7.4HP to 5HP).
- Power consumption decreased from 1.39kW/hr to 0.32kW/hr, achieving 77% energy savings.
-
Temperature rise, vibration, and current values all significantly decreased based on actual measurements.
- The vibration value dropped from 4.0μ to 3.0μ.
- The new system also contributes to 70L less oil consumption per oil change.
-
There have been no maintenance records since the upgrade.
※ The reduced oil tank size leads to lighter weight and indirectly lowers carbon emissions.
※ Zero maintenance means zero service costs, saving company expenses.
Item
|
|
AnyPower Vane Pump Power Unit
|
Power consumption per hour |
|
1.39kw-h |
Room Temperature |
24℃ | 28℃ |
Fluid Temperature |
26℃ | 36℃ |
Rise of Temperature |
|
8℃ |
Tank size | 130L | |
Motor capacity |
3.7kw-10P | 5.5kw-4P |
Vibration |
|
4μ |
SPL |
|
71db |
Current value R |
0.95A | 6.52A |
Current value S |
0.55A | 7.22A |
Current value T |
0.90A |
8.02A |
Servo hydraulic unit saves
77
%
energy than Piston type hydraulic unit
Background
- Air compressor manufacturing plant
- First time adopting an energy-saving hydraulic unit.
Point
- The tank size was reduced from 20L to 15L.
- The motor was reduced from 2HP to 1HP.
- Improved temperature rise, noise levels, and vibration values were observed.
- Since its delivery in 2019, it has operated for over 25,000 hours.
- Energy-saving efficiency reached 80%.
※ Although the initial purchase cost is higher than traditional options, the electricity bill has already been recouped.
※ Zero maintenance means zero service costs, saving company expenses.
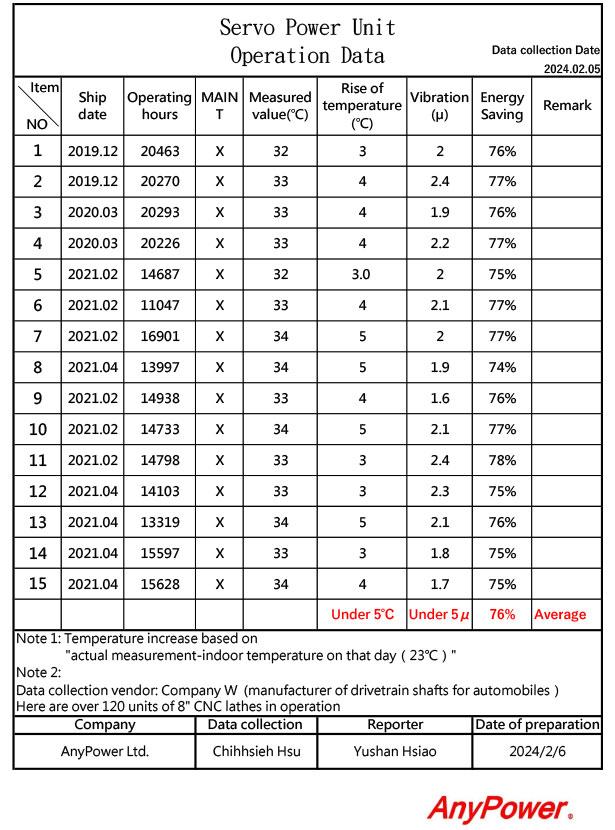
Testing Period:
From 1 pm March 1, 2018
To 11am Sep 6, 2018
Total operated 4088 hours
Total power consumption: 665.8 kwh (0.163 kwh per hour)
24 hours operation test (Mon to Sat)
Produce 1 component in 52 seconds.
Average producing 48 component in one hour
takes Servo hydraulic unit 0.16 kwh
and takes piston type hydraulic unit 0.68 kwh.
Conclusion: Servo hydraulic unit saves 76% energy than piston type hydraulic unit
Item
|
|
AnyPower Piston Pump Power Unit
|
Power consumption per hour |
|
0.68kw-h |
Room Temperature |
29℃ | 29℃ |
Fluid Temperature |
31℃ | 37℃ |
Rise of Temperature |
|
8℃ |
Motor Temperature |
33℃ | 43.5℃ |
Pump Temperature |
31℃ | 43.5℃ |
Vibration |
|
3μ |
SPL |
|
69db |
Current value R |
0.41A | 2.82A |
Current value S |
0.22A | 2.51A |
Current value T |
0.30A |
2.88A |
Servo hydraulic unit saves
80
%
energy than Piston type hydraulic unit
Background
- Test Machine: Horizontal Machining Center.
- The machine underwent maintenance and had Anypower servo hydraulic units installed.
Point
- The size of the oil tank for the old hydraulic equipment was reduced from 151L to 60L.
- The motor for the old hydraulic equipment was reduced from 7.5HP to 5HP.
- Temperature rise, vibration values, and current values all decreased according to actual measurements.
- The vibration value for the old hydraulic equipment decreased from 8.5u to 3.8u.
- There have been no maintenance records to date.
※ The reduced oil tank size leads to lighter weight and indirectly lowers carbon emissions.
※ Zero maintenance means zero service costs, saving company expenses.
Item
|
|
AnyPower Piston Pump Power Unit
|
Power consumption per hour |
|
0.68kw-h |
Room Temperature |
29℃ | 29℃ |
Fluid Temperature |
31℃ | 37℃ |
Rise of Temperature |
|
8℃ |
Motor Temperature |
33℃ | 43.5℃ |
Pump Temperature |
31℃ | 43.5℃ |
Vibration |
|
3μ |
SPL |
|
69db |
Current value R |
0.41A | 2.82A |
Current value S |
0.22A | 2.51A |
Current value T |
0.30A |
2.88A |
Servo hydraulic unit saves
80
%
energy than Piston type hydraulic unit
Background
- Company P purchased two machines from Japan's Company M.
- Both machines were originally equipped with traditional hydraulic units from Anypower. One of them was replaced with AnyPower servo hydraulic units.
Point
- The tank size was reduced from 20L to 15L.
- The motor was reduced from 2HP to 1HP.
- Improved temperature rise, noise levels, and vibration values were observed.
- Since the replacement with servo hydraulic units in 2019, there have been no maintenance records.
- Energy-saving efficiency reached 79%.
Item
|
|
Vane Pump Power Unit
|
Power consumption per hour |
|
0.7kw-h |
Room Temperature |
29℃ | 28℃ |
Fluid Temperature |
30℃ | 39℃ |
Rise of Temperature |
|
11℃ |
Motor Temperature |
34℃ | 45℃ |
Pump Temperature |
31℃ | 45℃ |
Vibration |
|
3.5μ |
SPL |
|
70db |
Current value R |
0.43A | 2.92A |
Current value S |
0.20A | 2.55A |
Current value T |
0.32A |
2.90A |